Understanding Downhole Filters: Enhanced Performance in Drilling Applications
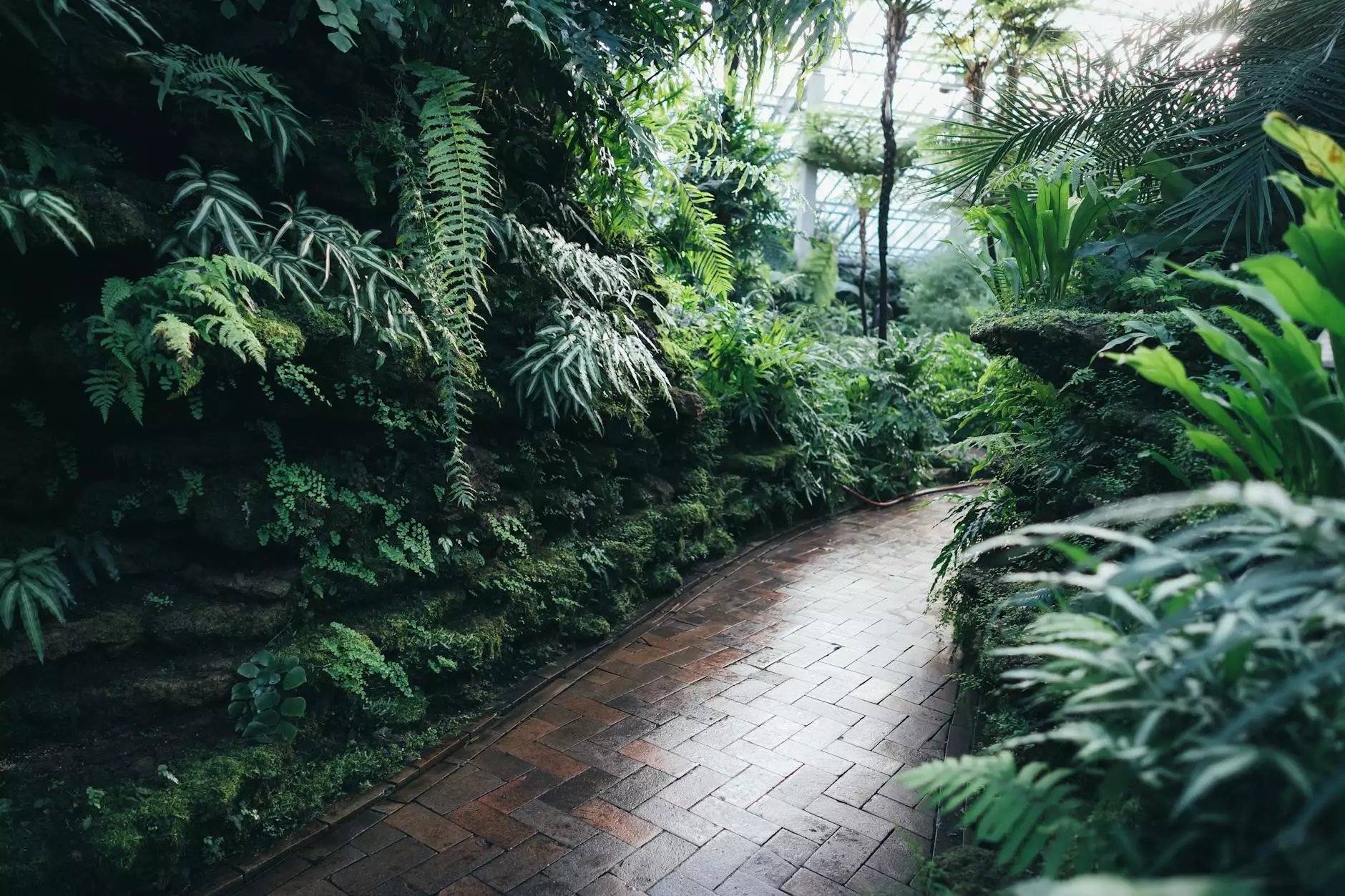
In the ever-evolving landscape of drilling technology, the importance of downhole filters cannot be overstated. These specialized devices play a crucial role in maintaining the integrity and efficiency of drilling operations, ensuring both safety and optimal performance in various geological conditions. This article will explore the intricacies of downhole filters, their components, benefits, and how they contribute to successful drilling operations, particularly for businesses in building supplies and machine & tool rental sectors, like Maverick Drilling.
What are Downhole Filters?
Downhole filters are specialized devices used in drilling applications to filter out unwanted particles and debris from the drilling fluids. They are essential for protecting the drilling equipment and ensuring that the fluid used during drilling remains clean. This is vital because contaminated drilling fluids can lead to system failures, increased wear on equipment, and ultimately higher costs for drilling operations.
The Anatomy of Downhole Filters
Understanding the components of downhole filters is key to appreciating their functionality. Here are the main parts:
- Filter Element: The core component that captures solids and contaminants as the drilling fluid passes through.
- Housing: The structure that encases the filter element, providing a robust unit that can withstand high pressures and temperatures.
- End Caps: These secure the filter element in place and ensure a sealed environment to force fluids through the filter effectively.
- Inlet and Outlet Ports: These allow the drilling fluid to enter and exit the filter, facilitating continuous fluid flow during drilling.
The Importance of Downhole Filters in Drilling Operations
In today’s competitive market, the efficiency and reliability of drilling operations are paramount. Downhole filters play a significant role in that efficiency.
Protecting Equipment
One of the foremost benefits of using downhole filters is their ability to protect drilling equipment. By removing harmful particles and debris from the drilling fluid, filters reduce the risk of clogs and system malfunctions. This protection is crucial for expensive drilling rigs and tools, which can incur high repair costs if damaged by contaminated fluids.
Enhancing Drilling Performance
By ensuring that drilling fluids are kept clean, downhole filters help to maximize the efficiency of the drilling process. Clean fluids can better lubricate and cool the drill bit, enhancing its performance and longevity. This leads to faster drilling times and reduced operational costs, making a significant impact on a company’s bottom line.
Improving Fluid Properties
Downhole filters also contribute to maintaining the desired properties of drilling fluids. By filtering out unwanted solids, they help maintain the viscosity and density of the drilling fluid, which are crucial for carrying cuttings to the surface and preventing issues such as wellbore instability.
Types of Downhole Filters
There are various types of downhole filters, each suited for specific drilling environments and applications:
- Wire Mesh Filters: Made from woven metal strands, these filters provide good durability and are used in various applications.
- String Wound Filters: These are wrapped with string or filaments to create a dense filter pack and are effective for fine particle removal.
- Sintered Filters: Constructed from powdered metals, sintered filters provide high filtration efficiency and are ideal for high-temperature applications.
- Cartridge Filters: These filters utilize a replaceable cartridge design, allowing for easy maintenance and replacement in the field.
Material Considerations for Downhole Filters
The choice of materials used in downhole filters significantly affects their performance and durability. Here are some common materials:
Stainless Steel
Known for its corrosion resistance, stainless steel is a popular choice for downhole filters, especially in harsh environments.
Polymeric Materials
These materials can provide excellent filtration properties while maintaining flexibility and light weight—beneficial for certain applications.
Composite Materials
Composite materials combine the benefits of metals and polymers, offering optimal filtration solutions while minimizing weight.
Applications of Downhole Filters
Downhole filters are utilized across various sectors in the drilling industry. Here are some notable applications:
Oil and Gas Exploration
In the oil and gas sector, downhole filters are crucial for maintaining the integrity of drilling fluids in diverse geological formations. They ensure that drilling operations proceed smoothly, minimizing downtime and maximizing productivity.
Water Well Drilling
For water well drilling, these filters help to clean the drilling fluid, ensuring optimal water quality and minimizing contamination risks.
Geothermal Energy Drilling
In geothermal projects, downhole filters play a vital role in managing thermal stability and operational safety, ensuring that the geothermal fluids remain clean and efficient.
Challenges with Downhole Filters
While downhole filters offer numerous advantages, there are challenges associated with their use:
Clogging
Over time, filters can become clogged with captured debris, which necessitates regular maintenance and replacement to avoid performance issues.
Cost Implications
The initial investment in high-quality downhole filters can be significant. However, this cost should be justified by the long-term savings realized through enhanced performance and reduced equipment wear.
The Future of Downhole Filters
The future of downhole filters in the drilling industry looks promising. Ongoing advancements in materials technology and filtration processes are expected to lead to more efficient and durable filters. Here are some emerging trends:
Smart Filters
With the rise of IoT (Internet of Things) technology, smart downhole filters equipped with sensors could provide real-time data on filter performance, helping operators make informed decisions and timely replacements.
Enhanced Filtration Technologies
Research is ongoing into new filtration technologies that could further enhance the efficiency and effectiveness of downhole filters, aiming to remove even smaller particles from drilling fluids.
Conclusion
In summary, downhole filters are a vital component in modern drilling operations, playing a crucial role in enhancing the effectiveness and safety of drilling projects. Their ability to protect equipment, improve drilling performance, and maintain fluid integrity is unmatched. For businesses in the drilling sector, particularly those catering to the building supplies and machine & tool rental markets, investing in quality downhole filters from reputable suppliers like Maverick Drilling is essential for operational success.
By understanding the benefits, types, applications, and future innovations surrounding downhole filters, companies can make informed decisions that foster growth and efficiency in the competitive drilling landscape.