Understanding Die Casting Mould Parts for Optimal Production
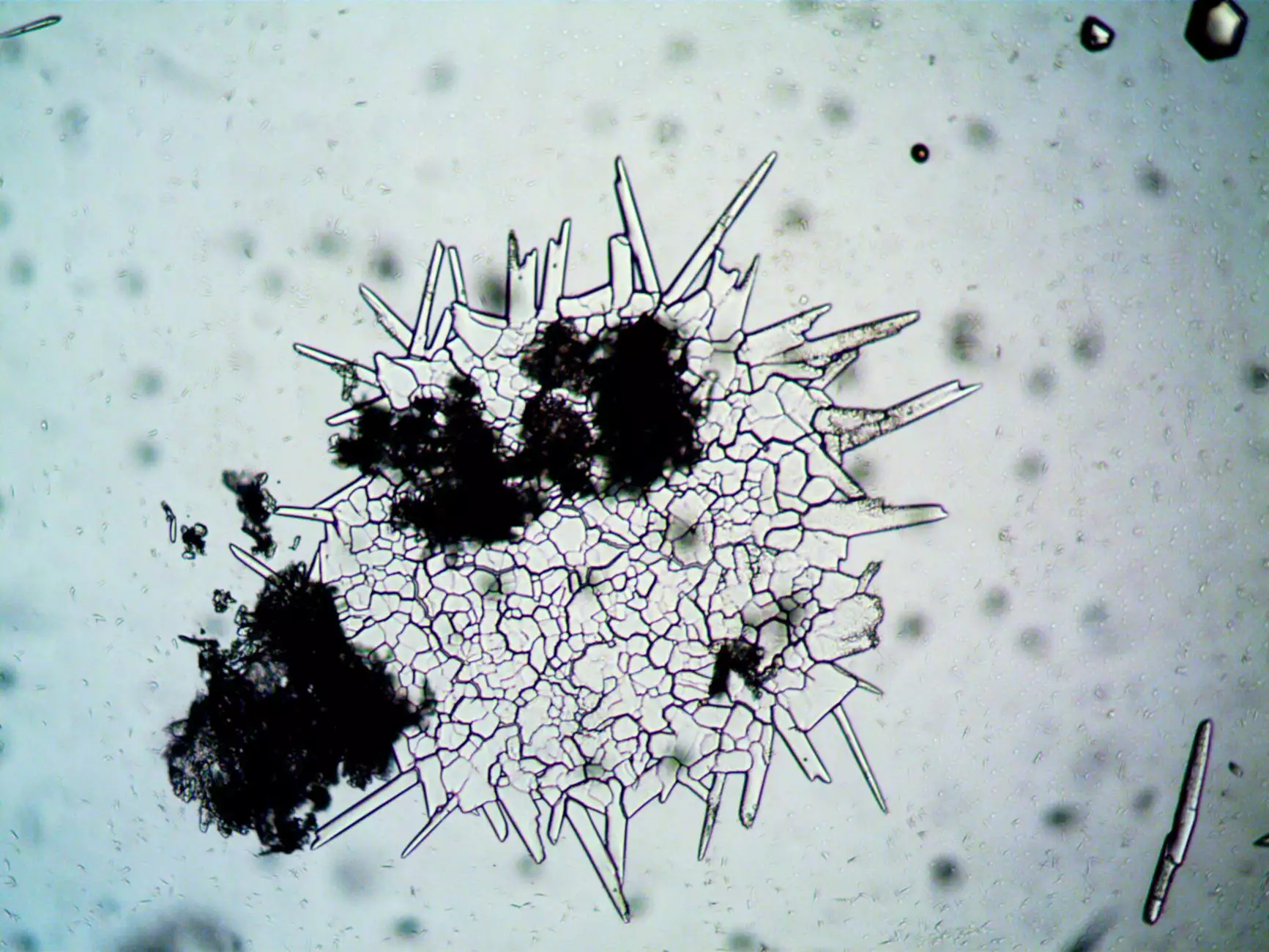
In the realm of metal fabrication, few processes stand out as prominently as die casting. This advanced manufacturing technique allows for the production of intricate shapes with exceptional precision. At the heart of this process are die casting mould parts, which play a crucial role in determining the quality, efficiency, and cost-effectiveness of the final product. In this comprehensive guide, we will explore the various facets of die casting mould parts and how they can be optimized to enhance business operations at deepmould.net.
The Essence of Die Casting
Before we delve into die casting mould parts, it's important to understand the die casting process itself. Die casting involves forcing molten metal into a mold cavity under high pressure. This process is not only efficient but also allows for the production of parts with very complex geometries. The cooling process occurs rapidly, leading to high production rates and consistency.
What Are Die Casting Mould Parts?
Die casting mould parts are the components that make up the mold used in the die casting process. These parts are designed to endure the extreme heat and pressure generated during casting. The quality of these mould parts directly influences the final product's quality, production costs, and time efficiency. The main types of die casting mould parts include:
- Core Inserts: These are used to create internal cavities within the casting.
- Cavities: The primary shapes that will dictate the outer dimensions of the final product.
- Cooling Channels: Channels that allow coolant to flow through, accelerating the cooling of the molten metal.
- Ejector Pins: These components assist in removing the finished product from the mold.
- Guide Pins and Bushings: These ensure accurate alignment of the mold halves during the injection process.
Material Selection for Mould Parts
The material used for die casting mould parts must withstand high temperatures and pressures, making the selection of appropriate materials vital. Typically, these materials include:
- Tool Steel: Known for its hardness and ability to retain its shape under pressure.
- Aluminum Alloys: Lightweight and good for thermal conductivity; often used for low-volume die casting.
- Hardened Steel: Offers excellent wear resistance, ideal for high-volume production.
- Maraging Steel: A type of ultra-high strength steel, providing both durability and toughness.
Choosing the right material is crucial as it impacts not only the production cost but also the lifespan of the mould parts and the quality of the castings produced.
Factors to Consider When Designing Mould Parts
When designing die casting mould parts, several factors come into play that can affect the end product:
- Design Complexity: More intricate designs can lead to complications in manufacturing and higher costs.
- Production Volume: Higher volumes often justify the investment in more durable and precise moulds.
- Thermal Properties: Understanding how different materials cool can help in planning effective cooling channels.
- Draft Angles: These angles facilitate easier ejection from the mould and are crucial for the successful casting.
How to Optimize Die Casting Mould Parts
Optimizing die casting mould parts is essential for enhancing production efficiency and reducing costs. Here are some strategies:
1. Implement Advanced CAD Software
Utilizing advanced Computer-Aided Design (CAD) software allows for more efficient and precise mold designs. CAD helps visualize the entire casting process, enabling designers to optimize the mould structure and cooling channels.
2. Utilize Simulation Technology
Before actual production, simulation technologies can predict how the molten metal will behave in the mould. This preemptive approach can help identify and address potential issues related to fill patterns, cooling, and shrinkage.
3. Invest in High-Quality Machining
The precision of the machining process used to create mould parts directly impacts their performance. Invest in high-quality machining services to ensure that components fit together perfectly, reducing the risk of defects.
4. Perform Regular Maintenance
Die casting mould parts require regular maintenance to prolong their lifecycle. Establishing a routine maintenance schedule can help identify wear and tear early, allowing for timely repairs or replacements.
Benefits of Using Quality Die Casting Mould Parts
Investing in high-quality die casting mould parts offers several benefits:
- Improved Product Quality: High-quality moulds lead to better precision and a more refined finish on the final product.
- Increased Production Efficiency: Optimized designs and effective cooling channels speed up the production process, resulting in higher output.
- Reduced Waste: Quality moulds reduce the incidence of defects, leading to less material waste and greater overall profitability.
- Longer Lifespan: Investing in durable materials and proper design prolongs the life of the moulds, reducing long-term costs.
Applications of Die Casting Mould Parts in Various Industries
Die casting is a versatile process utilized in a myriad of industries. The applications of die casting mould parts can be found in:
- Automotive: Parts like engine blocks, transmission housings, and structural components.
- Aerospace: Lightweight components used in aircraft for fuel efficiency.
- Consumer Electronics: Enclosures and internal components that require intricate designs.
- Medical Devices: Precise moulds for producing necessary medical tools and equipment.
- Home Appliances: Parts used in refrigerators, washing machines, and more that require robust production.
Future Trends in Die Casting Technologies
As industries evolve, so do the technologies behind die casting. Here are some emerging trends that could shape the future of die casting mould parts:
1. Automation and Robotics
Integrating automation and robotics into die casting systems can drastically enhance production speed and precision, as well as create safer working environments.
2. Innovative Materials
New materials are being developed that offer higher strength-to-weight ratios and better thermal properties, thereby enhancing the die casting process.
3. Eco-Friendly Practices
With increasing emphasis on sustainability, there is a push towards more environmentally friendly mould materials and processes that minimize waste and energy consumption.
Conclusion
In conclusion, die casting mould parts are fundamental in the manufacturing landscape, especially for businesses dealing with metal fabrication. As the industry continues to evolve, understanding how to optimize these mould parts can lead to significant competitive advantages. By investing in quality materials, leveraging advanced technologies, and adhering to best practices, businesses like deepmould.net can enhance their production capabilities, ultimately leading to superior products and increased profitability.