Electrical Plastic Molding: Transforming Industries with Innovation
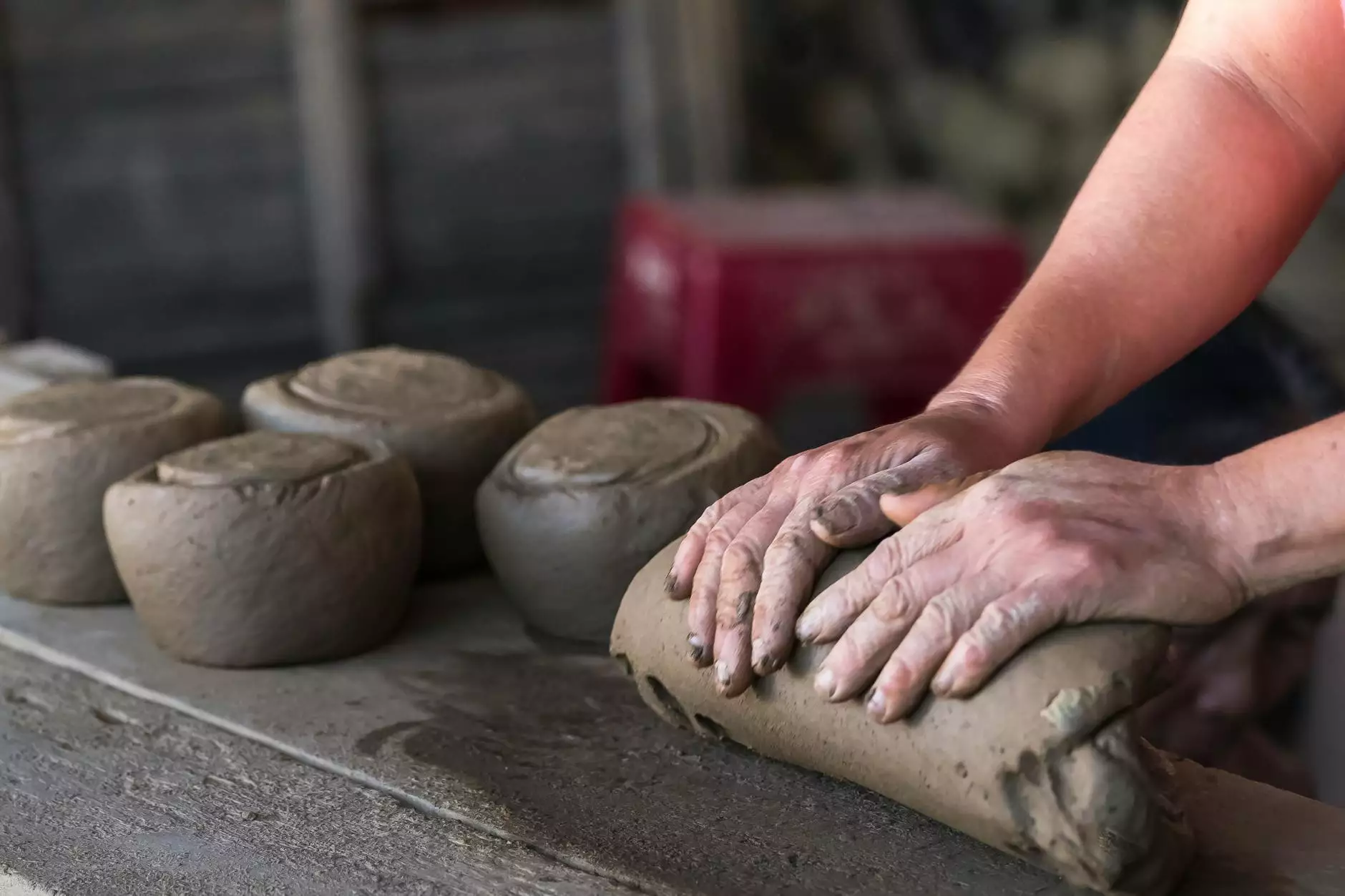
In the fast-paced world of manufacturing, Electrical Plastic Molding stands out as a critical component driving innovation in various sectors. From consumer electronics to automotive production, the demands for precise, durable, and cost-effective components have never been greater. This article explores the ins and outs of electrical plastic molding and its importance in today's manufacturing landscape.
Understanding Electrical Plastic Molding
Electrical plastic molding is a sophisticated process that combines plastic injection molding techniques with electrical component production. It enables manufacturers to create intricate plastic parts that can accommodate electronic components, reducing assembly times and improving efficiency. This process is essential in industries where space and weight are paramount.
The Process of Electrical Plastic Molding
The process of electrical plastic molding involves several key steps:
- Design: The journey begins with meticulous design, often using CAD software to create detailed models that cater to specific electronic requirements.
- Material Selection: Choosing the right thermoplastics is crucial. Materials must not only provide structural integrity but also possess the necessary electrical properties.
- Molding: The heart of the operation. Plastic is heated until molten and injected into a mold where it takes shape. This step often incorporates metal inserts for electrical connections.
- Curing and Finishing: After cooling, the parts may undergo additional processes, such as surface treatments or secondary machining, to achieve the desired specifications.
The Benefits of Electrical Plastic Molding
Organizations looking to enhance their production capabilities can reap numerous benefits from electrical plastic molding:
- Cost Efficiency: By combining processes, manufacturers can save significantly on labor and assembly costs.
- Design Flexibility: Complex geometries and integrated components are possible, allowing for innovative designs that were previously unattainable.
- Reduced Assembly Time: Electrical plastic molded components can be produced as a single part rather than multiple components, thus minimizing assembly time and potential points of failure.
- Enhanced Performance: The right choice of polymers can lead to better dielectric properties, thermal stability, and overall performance of the end product.
Electrical Properties of Plastics
One of the most significant advantages of using plastics in electrical applications is their dielectric properties. These properties ensure that components can operate effectively without short-circuiting or losing efficiency. Some key aspects include:
- Insulation: Plastics are excellent insulators, making them ideal for various electrical applications.
- Thermal Stability: Certain polymers can withstand high temperatures, which is crucial for electronic devices that generate heat.
- Lightweight: Plastics significantly reduce weight compared to metals, benefiting applications where weight savings impact performance.
Applications of Electrical Plastic Molding
Electrical plastic molding is integral to numerous industries, each with unique requirements:
1. Consumer Electronics
Devices like smartphones, tablets, and wearables heavily rely on plastic molded components for casings, connectors, and internal supports. The integration of electrical components into molded parts reduces space and enhances device performance.
2. Automotive Industry
The automotive sector demands high-performance materials that are lightweight yet robust. Electrical plastic molding enables the production of components like dashboard controls and sensor housings, enhancing vehicle efficiency and safety.
3. Medical Devices
In medical applications, precision is paramount. Electrical plastic molding allows the creation of components for diagnostic and treatment equipment, ensuring reliability and safety in life-critical situations.
4. Telecommunications
The telecommunications infrastructure heavily depends on molded plastic parts for routers, switches, and protective casings, emphasizing durability and performance in various environments.
5. Aerospace Components
Aerospace applications require materials that withstand extreme conditions while maintaining performance. Electrical plastic molding is used to create lightweight housings and components that contribute to fuel efficiency.
Choosing the Right Partner for Electrical Plastic Molding
With the increasing complexity of designs and the importance of quality, selecting the right manufacturing partner is critical. Here’s what you should consider:
- Experience: Choose a supplier with a proven track record in electrical plastic molding to ensure quality and adherence to specifications.
- Technology: Advanced equipment and technology can significantly impact the quality of the final product. Ensure your partner uses the latest molding technology.
- Material Expertise: A comprehensive understanding of material properties is critical for optimizing the performance of molded components.
- Customer Support: A supplier should provide robust customer support during the design, production, and post-production phases.
Sustainability in Electrical Plastic Molding
As industries move towards sustainable practices, electrical plastic molding is adapting to environmental concerns. Manufacturers are increasingly using:
- Recyclable Materials: The trend is shifting towards using recyclable polymers, reducing environmental impact.
- Energy-efficient Processes: Advancements in molding technology lead to lower energy consumption during production.
- Waste Minimization: Techniques such as precision molding reduce waste and enhance resource utilization.
The Future of Electrical Plastic Molding
The outlook for electrical plastic molding is bright, with continuous advancements in technology fueling innovation. The integration of smart manufacturing technologies such as 3D printing and automation is set to revolutionize the industry:
- Smart Manufacturing: The integration of IoT (Internet of Things) in manufacturing processes will enhance data acquisition and machine learning applications.
- Customization and Rapid Prototyping: 3D printing allows manufacturers to quickly prototype and customize designs before moving to mass production.
- Higher Efficiency: Automation will streamline operations, reduce costs, and improve product quality.
Conclusion
Electrical Plastic Molding is an essential technique shaping the future of numerous industries. By providing innovative solutions that combine efficiency, cost-effectiveness, and performance, businesses that embrace this technology can stay ahead in a competitive marketplace. As companies like deepmould.net continue to push the boundaries of what is possible in molding technology, the possibilities for electrical applications are limitless. The time to innovate with electrical plastic molding is now, positioning organizations for success in a rapidly evolving industrial landscape.
© 2023 deepmould.net. All rights reserved.